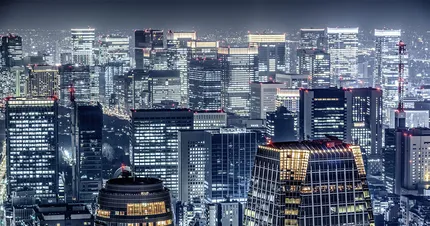
脱炭素社会への羅針盤「第7次エネルギー基本計画」 ~環境エネルギーライター・今村雅人が読み解く日本のエネルギー政策~
“定検工事期間短縮に貢献”に関する三菱重工パワーインダストリーの技術についてご紹介する全3回のシリーズ企画です。第一回は「フェーズドアレイUT法によるRT代替UT検査の現地適用」についてご紹介します。
火力発電用ボイラ及び産業用ボイラの定検工事においては期間の短縮が大きな課題です。現状、ボイラチューブ更新時の突合せ溶接部の検査手法として、放射線透過検査(以下、RT検査)を採用していますが、RT検査では、安全管理上、管理区域の設定や人払いなどの作業制約が発生します。また、溶接施工のステップとして、隣接する管と管の隙間及びパネル同士の隙間が非常に狭いことから、溶接不適合時の補修を考慮し1本毎に溶接・検査を繰返していく必要があり、RT検査ではその都度作業調整が必要となります。これらを背景に、工期短縮を目的としたRT検査に代わる検査手法の現地適用が急務でした。
発電用火力設備の技術基準により、外径115mm以下、板厚13mm以下の場合、RT検査を実施しなければならないわけではなくRT代替技術が適用可能です。そこで三菱日立パワーシステムズ株式会社(現三菱重工業㈱パワー事業部門)ではボイラチューブ突合せ溶接部に対するフェーズドアレイUT法による検査技術を開発し、三菱重工パワーインダストリー㈱が現地適用化を行いました。
フェーズドアレイUT法を用いた検査は、従来型の超音波検査法に代わり、様々なプラント診断における非破壊検査技術として採用されつつあります。三菱重工パワーインダストリー㈱は、ボイラ主要配管溶接部の欠陥検出、管内面の減肉状況の把握などボイラ各部の検査において、フェーズドアレイUT技術の現地適用に取り組み、経験と実績を積み重ねてきました。図1にフェーズドアレイUT装置の外観、図2にフェーズドアレイUT法の原理、図3に溶接部への超音波入射状況とその探傷画像をご紹介します。
フェーズドアレイUT法の特徴として、任意の位置への集束点の設定及び高感度化ができることから、後でご紹介する減衰の大きな材料であるオーステナイト系ステンレス鋼(SUS材)溶接部の検査にも適しています。また、従来型の超音波探傷器の出力信号より情報量が多く、視覚的に理解しやすいセクタースキャンによる断面画像(Bスキャン)表示が可能なため、溶接部内の欠陥エコーとその他の形状エコーとの識別がその場で容易にできます。
RT代替UT用プローブは、三菱重工業株式会社 総合研究所及び旧MHPS(現三菱重工業㈱パワー事業部門)の協力のもと、当社が製作を担当しました。図4にRT代替UT用プローブの外観をご紹介します。
検査対象となる部位は、過熱器管及び再熱器管で、その多くにSUS材が用いられています。SUS材溶接部は、粗大な柱状晶組織であり、一般的な横波を発生するプローブでは、超音波の減衰及び伝搬経路の偏向が大きく、図5に示すような柱状晶組織での散乱による林状エコー(雑エコー)が発生し、欠陥エコーの識別が難しくなる場合が多いです。
このため、超音波の減衰、散乱などが比較的少ない縦波を発生するプローブを採用することにしました。
さらに、図6の超音波入射状況が示すように、セクタースキャン(超音波ビームの方向制御)による検査では原理的に溶接部表面近傍の欠陥を捉えることが難しいため、表層部のみ伝搬するクリーピング波プローブ(表面及び表面近傍のキズの検出)を併用し、溶接部の全領域が確認できるようにしました。
図7に某火力発電所にてフェーズドアレイUT法によるRT代替UT検査を実施した再熱器管更新部溶接箇所の外観状況をご紹介します。隣接する管と管との隙間が非常に狭いため(最小隙間:18.5 mm)、プローブの高さを考慮しつつ、管径・管厚さに応じた最も反射効率の高い超音波ビームが形成されるように、あらかじめソフト上でのビームシミュレーションを行い、プローブを製作しました。
過熱器管、再熱器管などの小径管に関して、特にSUS材溶接部の超音波探傷試験方法については、まだ研究途上であり、規格化されたものがありません。そのため、RT代替UTの評価基準として、RT検査のJIS 規格(JIS Z 3104/3106 の1類)をベースとした社内基準を作成し適用することにしました。RT代替UT適用管を対象にRT検査規格で規定される許容きず点数(寸法)であるφ1.0mmのブローホールを模擬したφ1.0 mm横穴及び開先面の融合不良などを模擬したスリットを加工した検証用試験片を用いて、UTの検出性能の確認と評価基準の策定を行いました。
図8は検証用試験片の模擬欠陥加工図です。図9に示す欠陥からの反射エコーレベルで判断し、管の厚さ方向及び欠陥と溶接部との相対的な位置におけるエコー強度(高さ)の関係図を作成し、その評価レベルを超える欠陥を補修対象としました。
現地更新工事における検査体制として1チーム当たり2名(UT検査員+PC操作・記録員)で行い、検査員数及び工程に合わせてチーム数を決定します。フェーズドアレイUT装置自体が特殊検査装置であるため、有識者から教育と訓練を受け、検査遂行に必要な技量を有する検査員が対応します。また、工事は期間短縮のために溶接士含め原則昼夜交代による24時間体制で行いました。
RT代替UT検査の実機検査フローを図10にご紹介します。評価レベルを超える欠陥を検出した場合は、補修範囲のマーキングを行い、随時溶接補修し再検査を行っていきます。RT検査のような溶接補修後に再度、人払いを行って撮影し、現像・再評価を待って次工程に進む等の時間調整の必要はなく、補修後の再検査と評価が即座もしくは並行してできることがメリットです。
表1に旧MHPS(現三菱重工業㈱パワー事業部門)火力発電用ボイラ及び産業用ボイラ更新管溶接部へのRT代替UTの適用実績、表2に代表3プラント(表1のC、D、E)の工程短縮効果をご紹介します。表2に示すように、検査とその他工事に関わる作業が24 時間同時進行可能なため、RT検査に対してRT代替UT検査の工程短縮効果は大きいと考えられます。
ボイラチューブ更新時の突合せ溶接部のRT検査の代替としたUTプローブを製作及びフェーズドアレイUT法による検査技術を現地にて適用し、ボイラチューブ更新作業の短縮に寄与することができました。現状はブローホールなどの球状欠陥と融合不良や溶込み不良などの面状欠陥との識別が難しく、面状欠陥については微細欠陥を過大評価する傾向にあります。安全サイドに評価するという意味では品質管理上は、問題ないと考えられますが欠陥の検出率(=溶接補修率)が作業工程にも大きく影響することから今後の課題として、欠陥性状の識別・評価精度の向上を図っていきます。“定検工事期間短縮に貢献”シリーズ第二回は「回収ボイラ炉底管の水張りUT検査技術」です。
出典:『MHPS-IDS技報VOL.4(2019)』より
この記事に関連する三菱重工パワーインダストリーの技術情報(PDF)を無料でダウンロードいただけます。
※IDとパスワードが必要です。こちらのフォームからお申し込みください。